Advantages and disadvantages of 3D printed saddle
- Share
- publisher
- Danity
- Issue Time
- Nov 8,2024
Summary
Advantages and disadvantages of 3D printed saddle
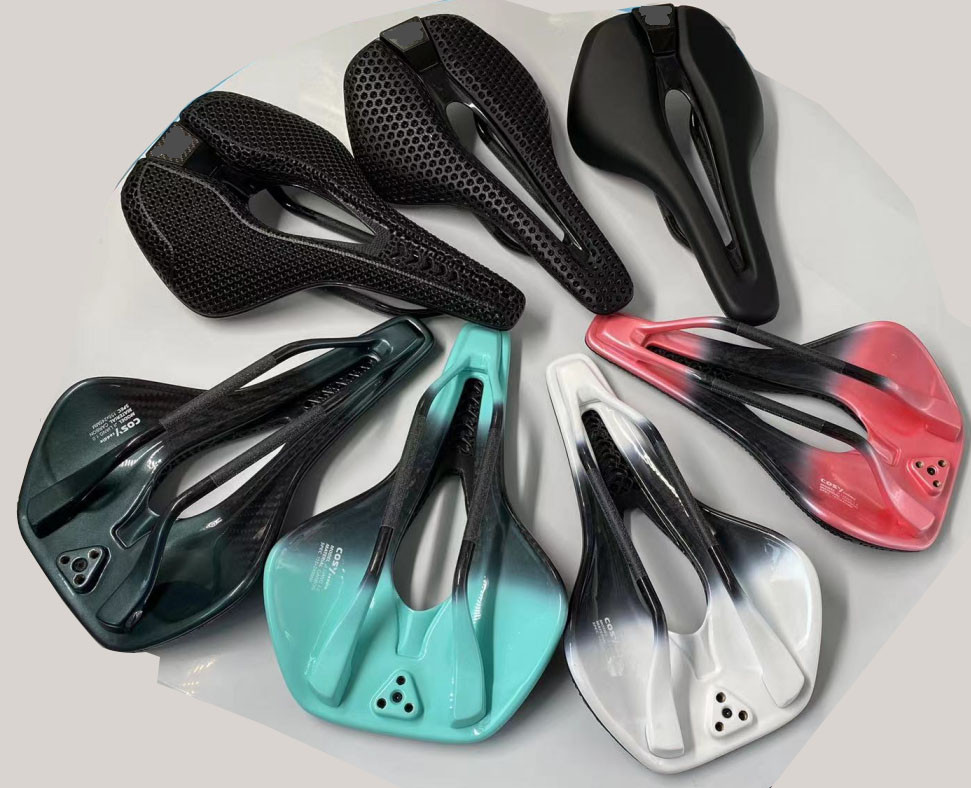
Disadvantages of 3D printed saddles: high cost, material limitations, and high design complexity.
1.High cost: The initial investment and operating costs of 3D printed saddles are relatively high, resulting in their prices typically being much higher than traditional saddles.
2.Material limitations: Currently, the types of materials available for 3D printing saddles are limited, and the cost of certain advanced materials such as certain metals or special plastics is high, which limits consumers' choices.
3.High design complexity: The design and manufacturing process of 3D printed saddles is relatively complex, requiring professional equipment and skills, which increases the difficulty of production.
The advantages of 3D printed saddle include comfort, lightweight, breathability, shock absorption, material durability, and high production efficiency.
1.Comfort: The 3D printed saddle uses advanced materials and technology to provide excellent comfort. For example, using titanium alloy rails not only ensures the durability of the saddle, but also provides excellent comfort, whether it is mountain riding or daily cycling, it can maintain a healthy riding posture. In addition, the design of 3D printed saddles emphasizes ergonomics, achieving differentiated support areas through parametric design and mechanical simulation, providing more uniform pressure distribution, and reducing pressure on soft tissue.
2.Lightweight design: The 3D printed saddle adopts a lightweight design, which enhances structural strength through a lattice structure with mechanical design, reduces consumable consumption, and has a smaller volume and more unique shape. This design not only reduces weight, but also improves the durability and resilience of the saddle.
3.and shock absorption: 3D printed saddles typically use hollow lattice structures, which not only provide natural breathability and alleviate sweating during cycling, but also have good shock absorption effects. The lattice density varies in different regions, with softer front and back ends and harder middle, which can better disperse pressure and provide better support.
4.Material durability: The polymer materials used for 3D printing saddles, such as TPU (thermoplastic polyurethane), have high resilience and durability. TPU material can still maintain high resilience after 1 million fatigue tests, and there are fewer occurrences of delamination, fracture, damage, etc. in various environments, resulting in a longer service life.
5.Personalized customization: 3D printing technology makes the design and manufacturing of saddles more flexible, enabling personalized customization. Designers can adjust parameters and designs according to specific needs, iterate and optimize products quickly, and meet the needs of different users.
6.Production efficiency: 3D printing technology eliminates complex processes such as mold opening and pressing in traditional manufacturing, simplifies the production process, shortens new product development time, and reduces the cost of personalized customization
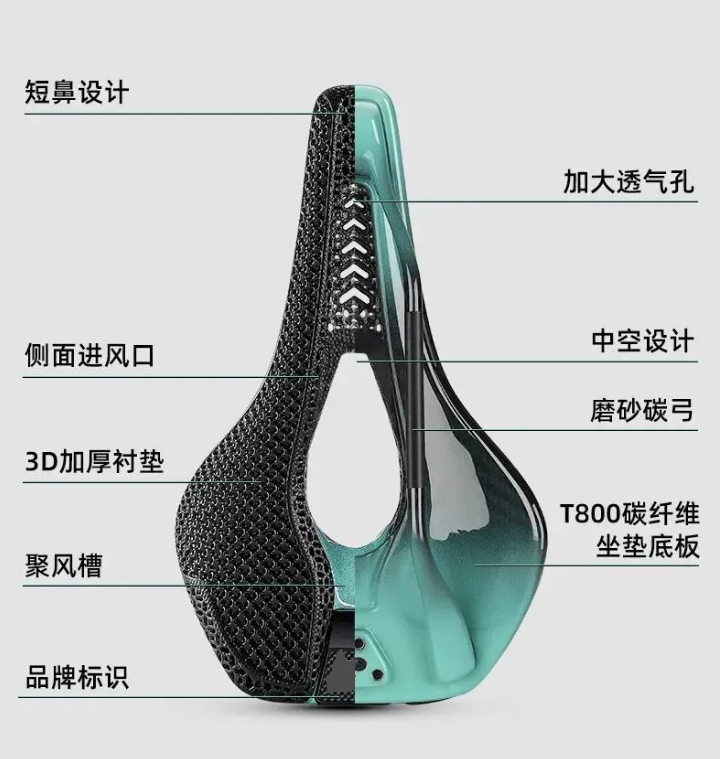
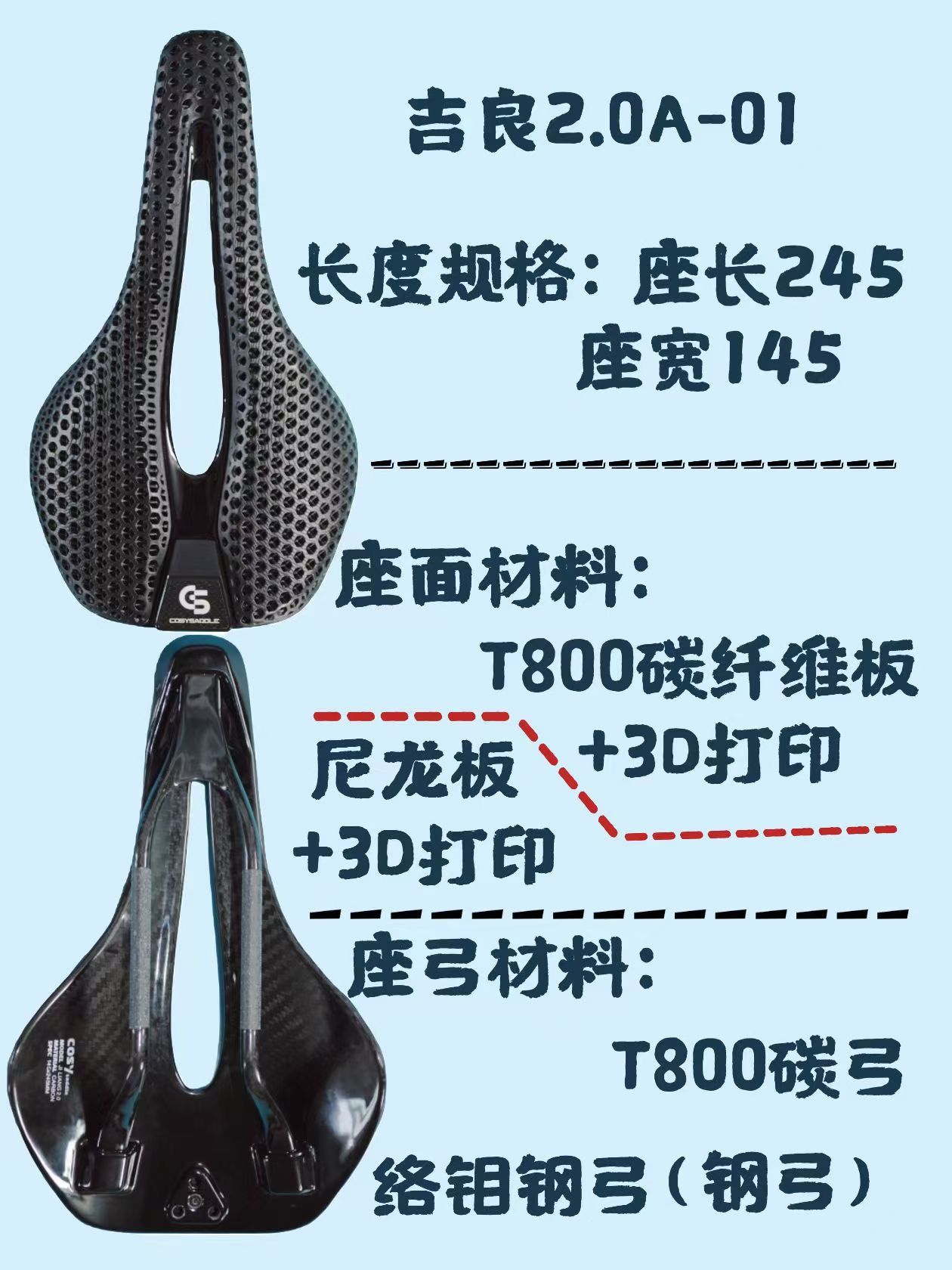
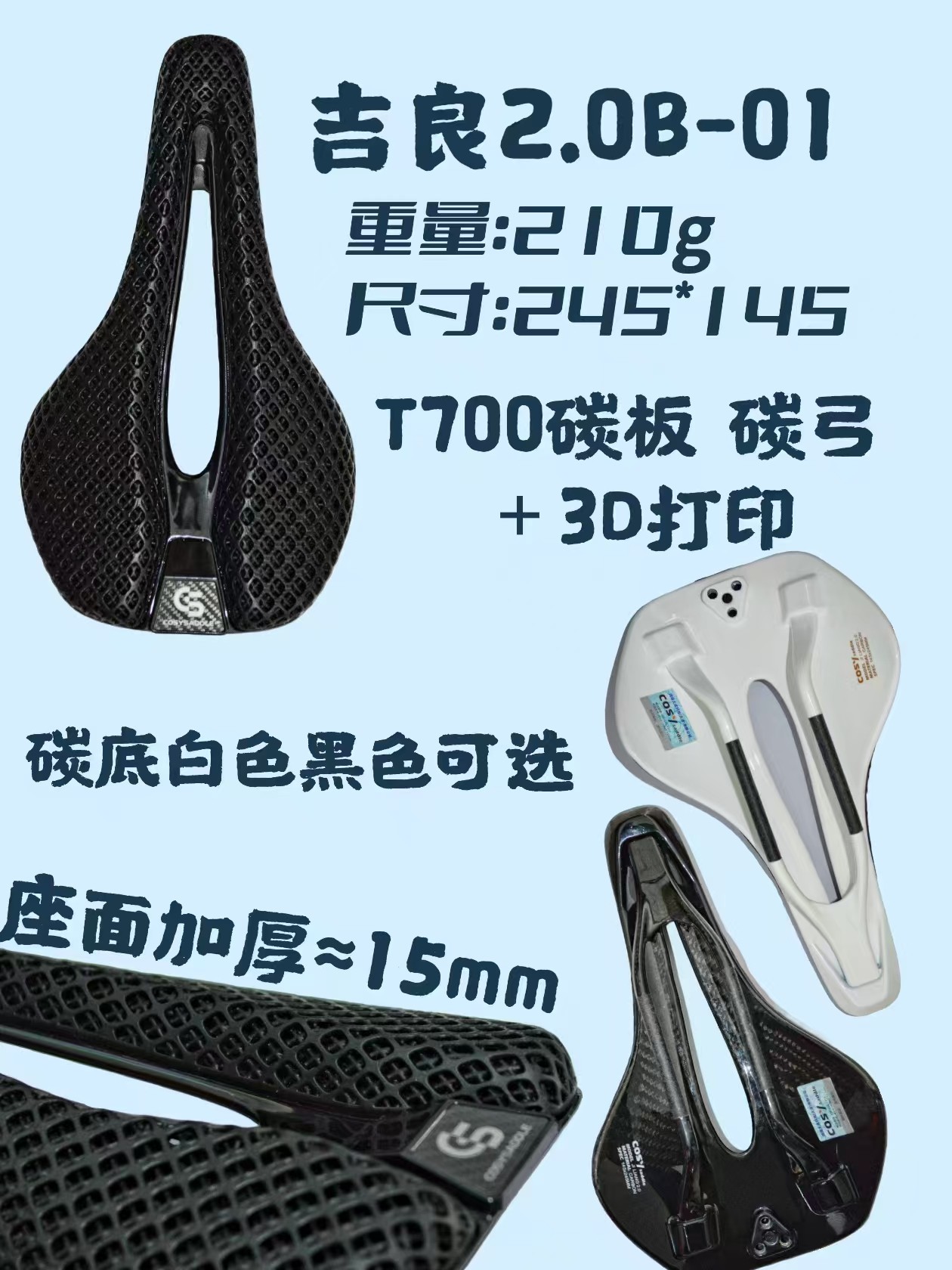
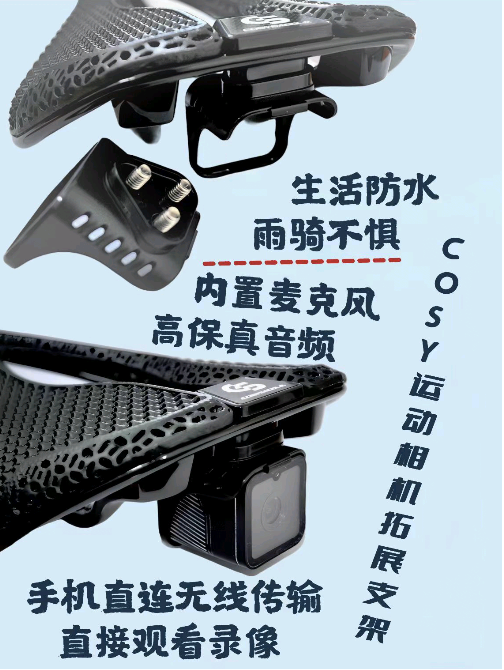