Synonymous with 3D printed bicycle saddles
- Share
- publisher
- Danity
- Issue Time
- Jun 13,2023
Summary
It can be said that "comfort", "breathable", "zonal shock absorption", and "no pressure" have become synonymous with 3D printed bicycle saddles.
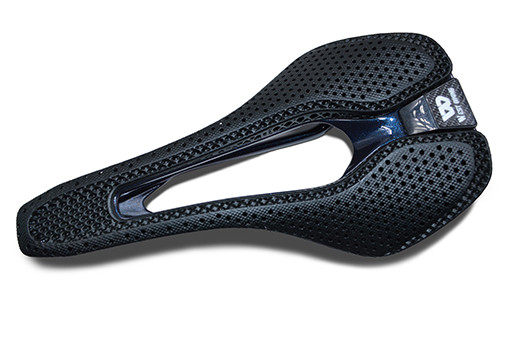
It can be said that "comfort", "breathable", "zonal shock absorption", and "no pressure" have become synonymous with 3D printed bicycle saddles. This is mainly due to parametric design and elastomer materials.
The design of the 3D printed saddle - the lattice structure is very special. The lattice structure is not only an aesthetic issue but also means that a precise seating feel can be achieved. We designed a partitioned lattice structure through an algorithm to achieve differentiated support areas.
3D printed saddles also require printing materials that are more durable, supportive and have high surface accuracy. The 3D printed saddle is made of high molecular polymer TPU material, and its elongation at break is as high as 680%. After 1 million tests, it can still be uncompromised, and has "as before" resilience. The TPU lattice cushion is less likely to be degummed, broken, damaged, etc. under the sun exposure, low temperature and other environments, and can withstand more severe environmental tests and has a longer service life. The bicycle saddle printed with TPU material has a matte texture and is lighter than traditional foam pads.
The saddle made by 3D printing only needs "one" process in the production process, without the need for large-scale mechanical equipment to open the mold and press the shape, and it can be directly printed and formed in one piece. Several processes are compressed into one - "printing". It not only shortens the time cost of new product development, but also reduces the cost of personalized customization.